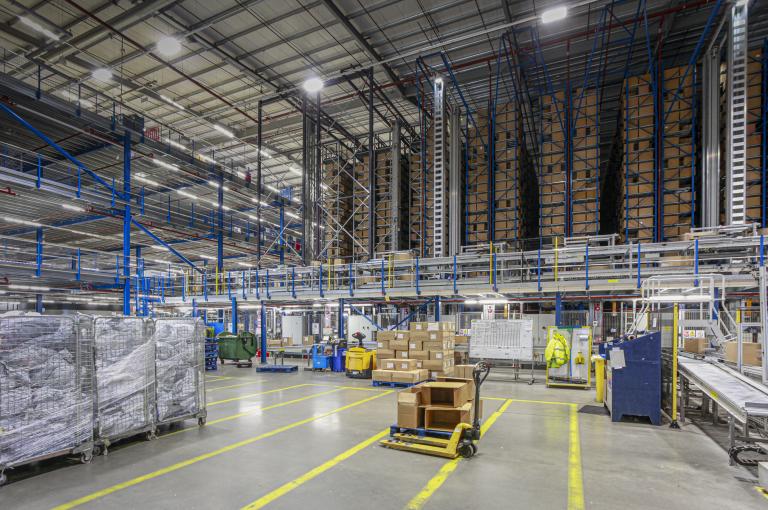
ASDA Warehouse, Washington
Get in touch
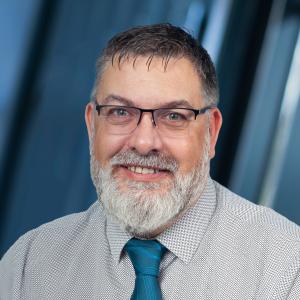
Summary
Construction of a three-storey mezzanine facility within the existing ASDA George distribution factory in Tyne and Wear
Robertson transformed the interior of a UK factory by building a three-storey structure within the existing facility, creating important additional capacity for ASDA.
Our customer was looking to expand their current storage and distribution facilities, and with spare height space in their factory, the simplest option was to build up, within the factory.
Works at the ASDA George distribution facility in Washington involved the removal of existing racking, construction of a new staircase, erection of temporary noise and dustproof screens, floor protection, the formation of the three-storey mezzanine structure, integrated M&E, and automation equipment installation.
28,000 m2
GIFA
3
storeys
24/7
operational factory
Operating on a live site
One of the challenges on this project was that the entire factory and all roads were live and fully operational throughout our construction works.
The site was set up to be operational 24 hours a day, seven days a week. This meant that consideration of factors such as noise, vibration, speed of installation and disruption to the surroundings were of paramount importance.
We shared the main entrance and exit with ASDA and had a dedicated gateman at the access point who controlled all vehicles and pedestrians in and out of the site.
Another challenge was that the Asda Warehouse project was at the height of Covid, and to mitigate this risk we implemented our strict guidelines for live sites, which all staff adhered to. We made provision for additional welfare facilities to ensure that social distancing rules were achieved, and additional contract cleaning was put in place.
Desks and tables were arranged to allow social distancing to be maintained and an anti-viral fogging machine was employed weekly.
Our attention to detail and meticulous planning meant that we could carry out construction in this challenging environment, delivering a first-class facility for our customer.
During the last 18 months we have had zero accidents onsite, due to the building work, which is a great result and a testament to the work done. Robertson has been helpful all the way through the project and have ensured that we remained operational without negative impact at the ASDA Washington depot.
Temporary dust and noise proofing
It was vital for ASDA that production and distribution was not affected in any way by our construction project which meant our team had to formulate an innovative approach to our work on site.
We arranged for temporary, bespoke screens to be hung from the existing roof and adjacent mezzanine structures, to maintain a safe working environment for the ASDA staff.
The screens were erected as one of the first operations on site and remained in place until each phase of the new mezzanine structure had been constructed, at which point they were moved and repositioned, so that work could be carried out in different areas of the facility.
Due to the enclosed nature of the works, there was the potential for excessive noise levels to be created by our operations. Where the noise could not be contained at source, acoustic enclosures were created to reduce the emitted sound.
Additional monitoring was created using the SoundEar2 noise measurement software which gives a visual representation of live sound and alerts operatives of where exposure levels are exceeded and for the hearing protection to be used.
It was also vital that there were no fumes from site plant, so all exhausts were fitted with special filters to protect those working in the warehouse.
Working with ASDA
Our team worked very closely with our customer, as we do on all projects.
A member of our site team – either the Project Manager or Site Manager – attended the ASDA morning meetings to understand their requirements, and to explain construction works taking place.
This high level of communication meant that everyone understood what was planned, and it allowed any issues arising to be identified and addressed quickly.
This meant that the entire project was delivered smoothly, without any accidents onsite associated with the build.
And our completed project gave our customer the additional capacity within the warehouse they needed, without production and distribution being affected.