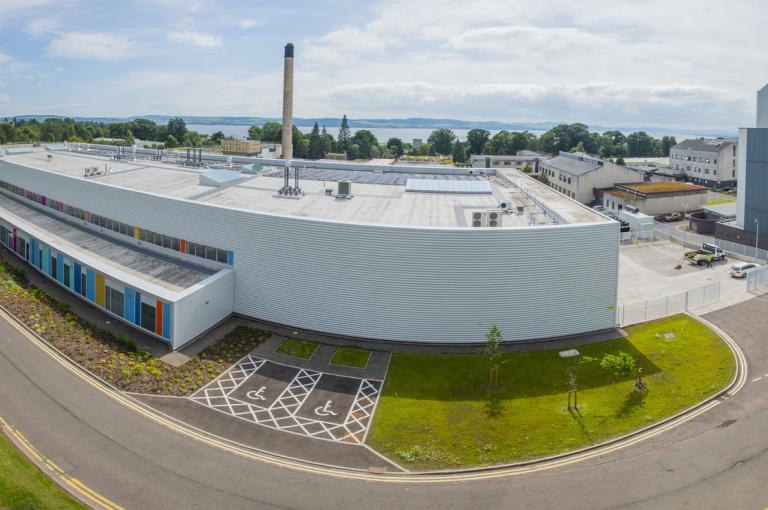
NHS Pharmaceutical ‘Specials’ facility
Get in touch
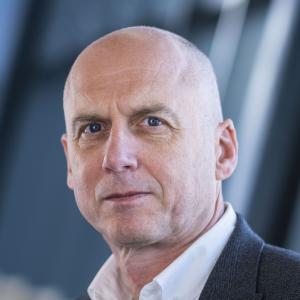
Summary
Manufacturing special medicines for patients in the UK
Robertson constructed the pharmaceutical ‘specials’ manufacturing facility on the grounds of Ninewells Hospital in Dundee for NHS Scotland. The project was delivered through the hub East Central Scotland framework.
The NHS Scotland Pharmaceutical 'Specials' Service manufactures medicines required when the available licensed medicines do not meet the specific needs of patients. Bringing together two former NHS Scotland manufacturing units based at Ninewells and the Western Infirmary Glasgow, the purpose-built facility also supports Research & Development in NHS Scotland and Scottish universities by providing medicines for use in clinical trials.
This is a hugely important and exciting opportunity for establishing a national pharmaceutical manufacturing service on the Ninewells site that will contribute to the care of NHS patients throughout the UK over the next 30 years and beyond.
A flexible, futureproof manufacturing facility
Our brief for the DBFM contract was to create a flexible design that provided NHS Scotland with a facility that could be easily upgraded to meet future new manufacturing processes, with minimal disruption. We worked closely with stakeholders to gain full understanding of all process flow requirements including people, product and waste.
Designing facilities to the required healthcare standards
We met all regulatory and legal requirements to ensure medicine, healthcare, technical and manufacturing compliance in each area. Cleanrooms were designed to cGMP standards with all grades having a high-quality vinyl finish applied to floors, walls and ceilings – also allowing the flexibility to upgrade areas in the future.
Non-cGMP support accommodation includes offices, warehouse, refrigerated cold rooms, canteen, collaborative spaces and meeting areas, all designed to provide a pleasant workspace and encourage high productivity.
The Building Management System and Validated Environmental Monitoring System include an environmental control with terminal high-efficiency particulate air filters and a highly regulated pressure regime; process utilities include water for injection, purified water, pure steam, breathing air, speciality gases, chilled water and steam – all fully compliant with requirements set by the Medicines and Healthcare products Regulatory Agency (MHRA).
Gallery
Keeping facilities operating
The building was designed with the flexibility to run 24/7. Robertson Facilities Management provides ongoing maintenance support so this critically important facility can keep operating efficiently at all times.