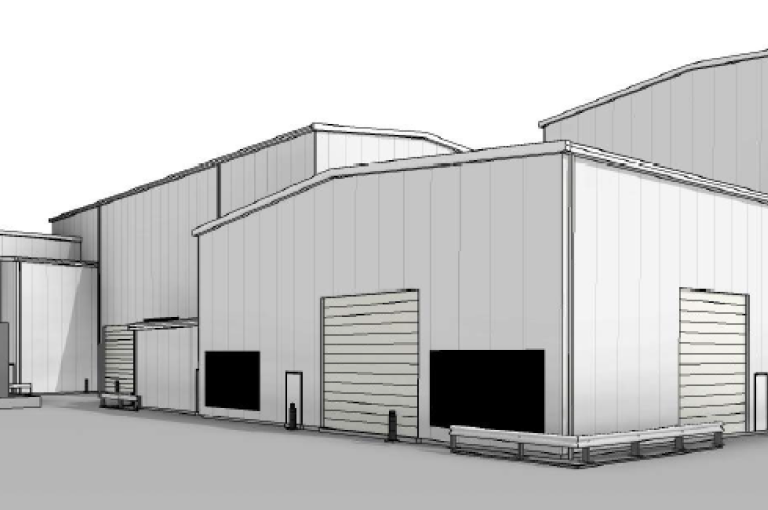
Essity Prudhoe Mill, Northumberland
Get in touch
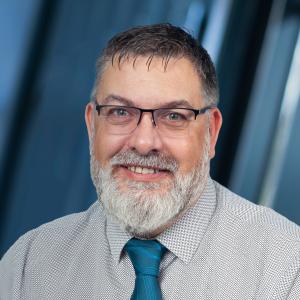
Summary
Building a multi-million recycling plant for paper manufacturing company Essity Prudhoe Mill
Robertson is constructing a brand-new recycling plant, securing a bright future and increased capabilities for our customer Essity Prudhoe Mill.
We will demolish the current 50-year-old Unifibres complex and replace it with a new building, housing recycling technology that will reduce energy costs and increase our customer's ability to make new products from recycled fibre.
2678m2
GIFA
435
tonnes of steel
4
building development
Creating a facility for the 21st century
We are constructing four buildings within the facility, adding capacity and capability for our customer.
The primary building will house the wet lap machine and waste area. This is also where the finished product will exit the building for collection and onward process through the plant.
The DEINK building is a two-storey structure which will house most of the process from wet product through to end product, feeding the wet lap machine. The building also connects to the external mezzanine tank area. Within the building there is an overhead crane on the first floor, covering the machines to allow for transfer of product, kit and maintenance, as well as assisting with the installation upon construction.
The third building is the Bunded Chemical Area where chemical storage tanks are held.
The final building is a Workshop and Steam Pressure Reduction room and will be constructed using a prefabricated GRP (Glass Reinforced Plastic) clad building method.
There will also be numerous internal and external mezzanine levels to service and support the plant equipment. These are a mixture of supported concrete deck floors and open mesh GRP grate flooring.
Operating on a live site
One of the challenges of this project is minimising disruption to operations during construction. The factory is in operation seven days per week and the client requires us to prevent any down time for Essity daily operations.
We have experience of working in many live environments, whether it be hospitals, schools, or factories. We work closely with our customer to understand their work routines and develop plans that will minimise any disruption.
Building capability
By completing this dramatic modernisation of Essity's facilities, our customer will be able to recycle lower-grade paper and board, enhancing their ability to segregate plastic and metal contaminants, reduce waste sent to landfill, and improve energy efficiency.
The introduction of this ground-breaking technology will also significantly reduce Essity's energy consumption, cutting their costs and improving their environmental credentials.
Their old Unifibres facility was at the end of its working life and this scale of investment secures the future of the mill, helping to meet the demand for their products, and will provide a more attractive and safer working environment for their employees.
The new recycling facility will also safeguard the long-term jobs of their workforce and create fresh opportunities by expanding their apprenticeship programme.